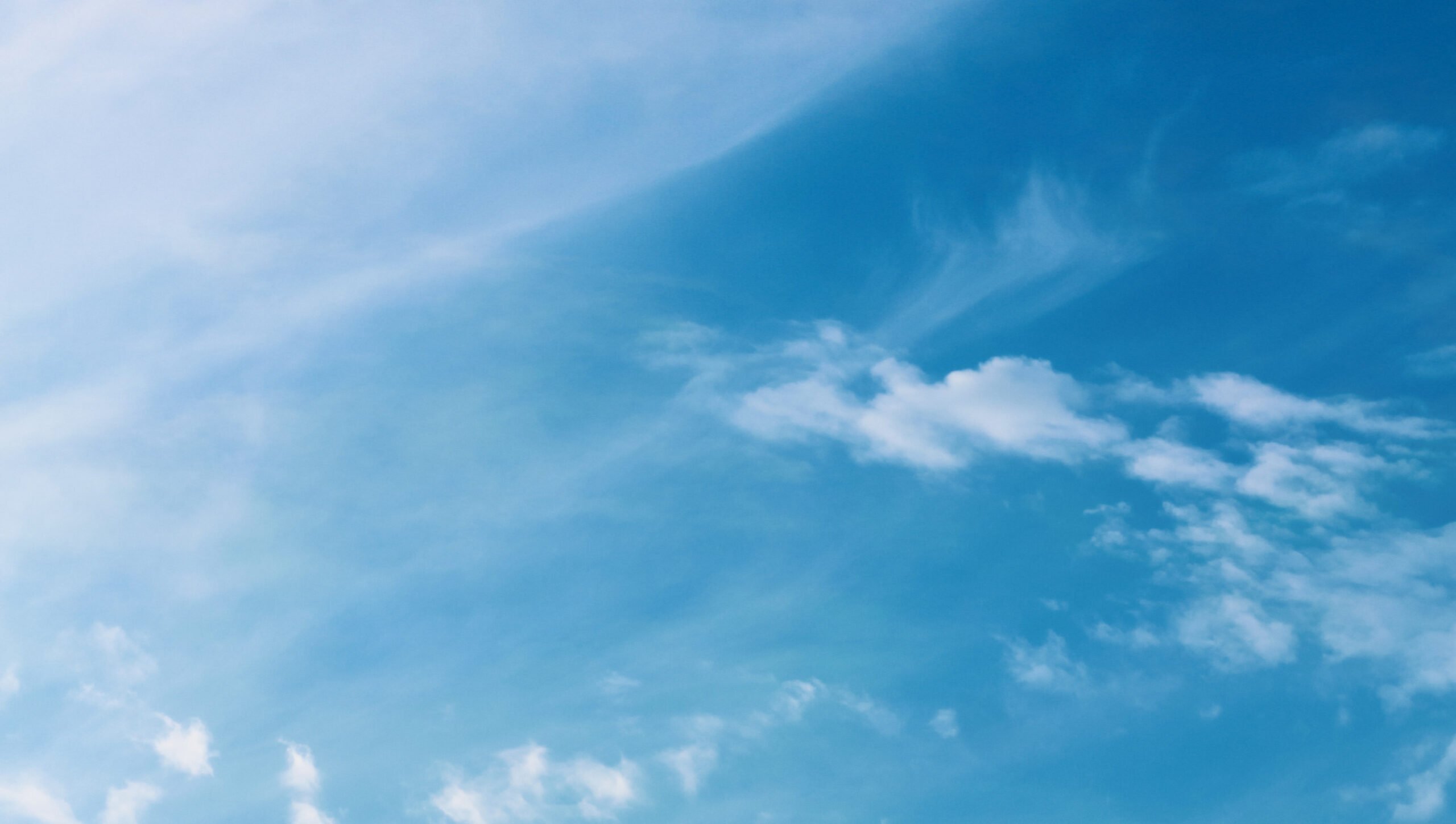

Thanks to the experience of its engineers and technicians EXUS has unrivalled expertise in Thermal Oxidiser technology.
Everything from initial investigation to final commissioning is kept in-house leading to the most cost-effective solution for our clients. Careful process review at the investigation and design phase means our solution is fully optimised to the application giving the lowest long-term running costs. Our Engineers aim for the highest thermal efficiencies for Recuperative Oxidisers and auto-thermal operation for Regenerative Oxidisers.
Exus’s Thermal Oxidisers Advantages
Gaseous effluent from various industrial processes can contain high levels of VOCs (Volatile Organic Compounds) or odours which have to be treated before discharge to atmosphere in order to meet prevailing regulations. The most effective and widely used solution for VOC and odour treatment is Thermal Oxidation. Pollutant gases are heated to high temperature in a combustion chamber in the presence of air and are fully oxidised before being discharged as a harmless gas.
Thermal Oxidisers are designed and manufactured to recover heat energy externally (Recuperative Oxidisers) or internally (Regenerative Oxidisers). Which of these types is most appropriate is usually dependent upon the composition and delivery volume of the polluted air and the concentration of VOCs. Modern Oxidisers can also incorporate adsorption technology concentration techniques, which can bring even the largest air volumes with very low solvent loadings within reach of economic operation.
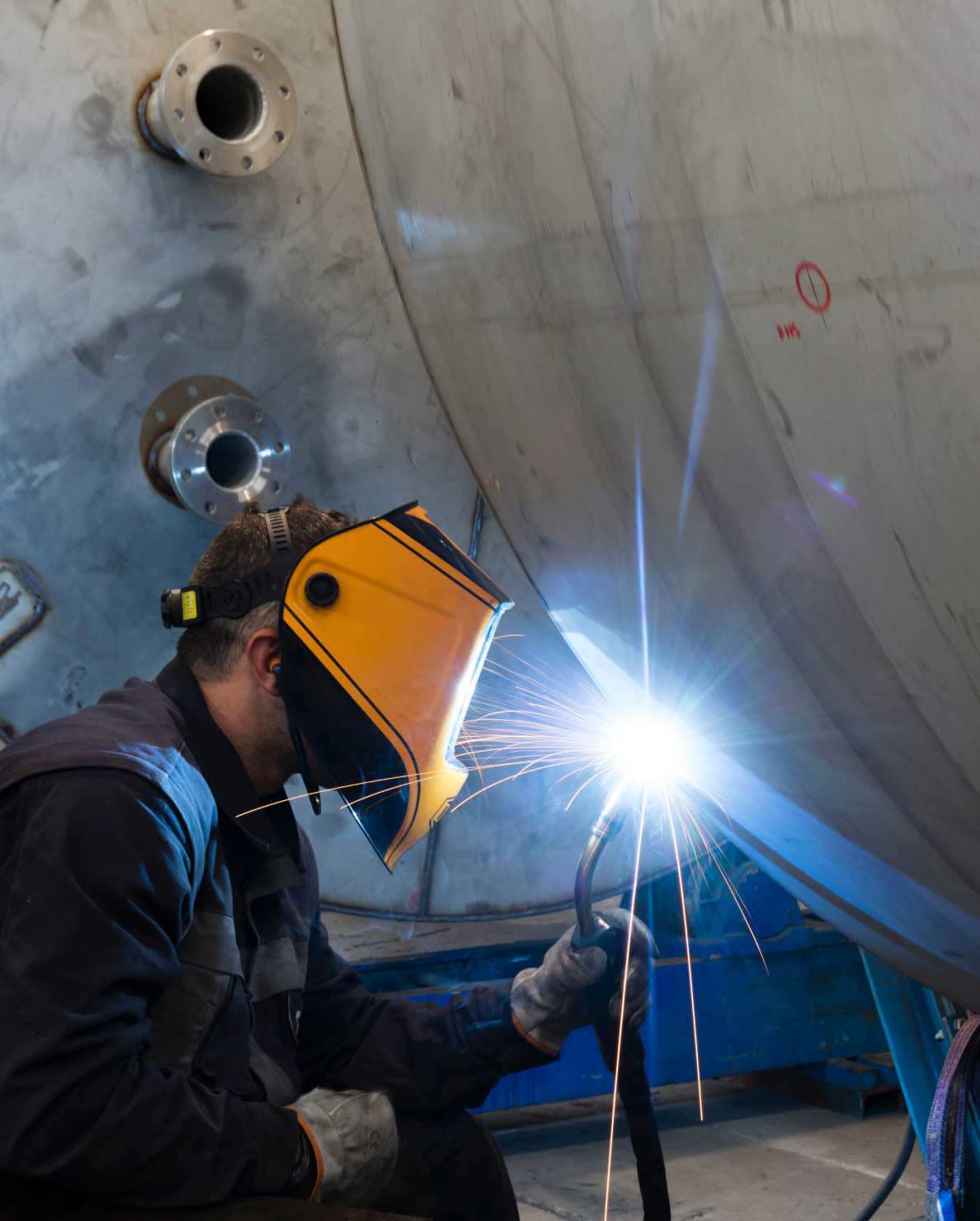
Regenerative Oxidisers
Regenerative Oxidisers are used where there is no requirement for heat recovery, or the amount of heat that can be recovered is too small to justify a Thermal Recovery Oxidiser. They are also well suited to processes that discharge high volumes of exhaust with relatively low VOC content.
Operating Principle
The VOC laden air from the process is drawn into the Oxidiser by means of a variable speed controlled effluent transport fan. The effluent is heated in the incoming tower, passed through the combustion chamber and cooled in the exit tower, each of which is filled with a specialist ceramic material.
To achieve the best thermal oxidation of the VOC, the following conditions must be met:
- Temperature between 750 and 950°C
- Dwell time of the effluent in the combustion chamber
- between 0.6 and 1 second
- Good turbulence for efficient mixing of effluent and oxygen
Advantages
- As effective as Recuperative Thermal Oxidiser, with lower NOx emissions
- Suited to high flow, low VOC content exhaust streams
- Continuous control of the emissions
- Simple management of operation
- Reduced maintenance
- Reduced gas/fuel consumption: the Regenerative Oxidiser can achieve auto-thermal conditions with very low concentrations of VOC
- Self-contained plant which does not produce waste or heat requiring subsequent recovery
- Range from 1,000 to 150,000 Nm³/h
Thermal or Recuperative Oxidisers
EXUS’S Thermal or Recuperative Oxidisers are targeted at industrial process where there is a combination of energy demand and effluent oxidation. These types of Thermal Oxidisers are mainly suitable for higher VOC concentrations and lower effluent flow rates.
Operating Principle
Pollutant gases are heated to high temperature – typically in excess of 800°C – in a combustion chamber for 0.6 – 2.0 seconds to fully oxidise them before being discharged to the atmosphere. Using Heat Recovery units, energy is recovered from the exhaust stream for reuse in the process or elsewhere, thereby reducing total operating costs.
Advantages
- Continuous control of emissions
- Simplicity of control and management
- Quick start up
- High energy recovery
- Safety and reliability with full hazard audit
- Range of effluent 500 to 30,000 Nm³/h
Deodorising Oxidisers
EXUS’S Deodorising Oxidisers are well known all over the world as the best available technology to abate odours generated by various production processes. They are specifically designed to suit the application and tailored to meet the particular requirements of each industrial process.
Operating Principle
Odours are typically processed temperatures of up to 950°C with a dwell time of approximately 0.8 seconds. A heat recovery boiler recovers energy from the flue gas stream and feeds it back to the process using steam or thermal fluid as the heat transfer medium. Dwell times are adjusted to suit process and local rules.
Advantages
- System overall efficiency over 99%
- Excellent odour abatement efficiency
- Possible use of animal tallow as primary fuel, with fuel oil or natural gas as a standby fuel
- Optimised investment and operating costs
Related pollutant
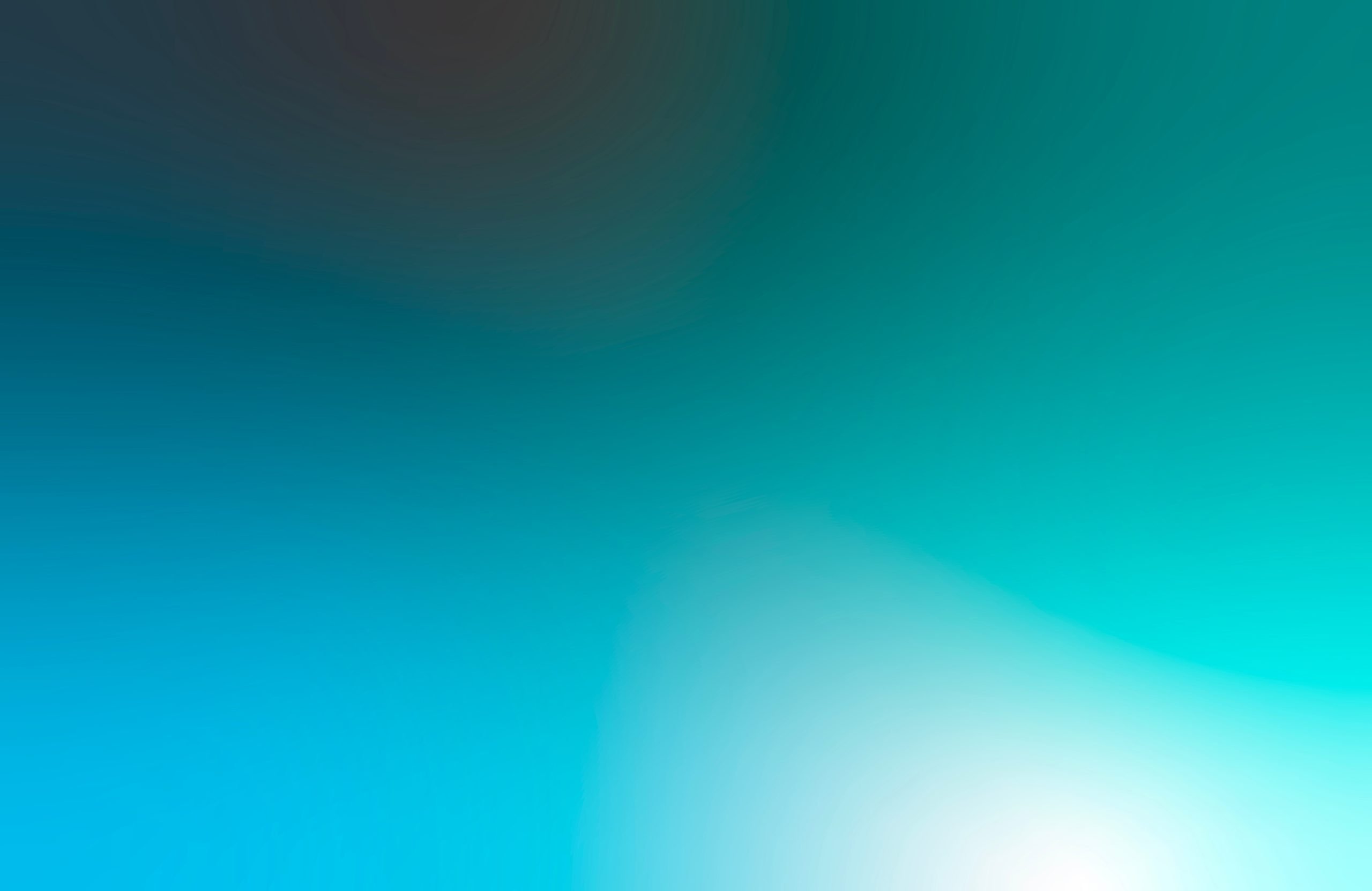
You can always count on tailor-made solutions with Exus. We will provide you with the solutions you need at all times.
Our technicians engage with every project, using their expertise and knowledge to design customised equipment for each case and customer.